In today’s highly competitive business landscape, efficiency and productivity are key to staying ahead of the game. One approach that has gained significant traction in various industries is 5S Lean Manufacturing. But what exactly is 5S, and why should you care about it? In this comprehensive guide, we will delve into the world of 5S Lean Manufacturing, exploring its origins, the five fundamental pillars, the numerous benefits, potential challenges, real-world success stories, and practical steps for implementation. By the end of this blog, you’ll have a clear understanding of 5S and why it should be on your organization’s radar.
Table of Contents
ToggleUnderstanding 5S Lean Manufacturing
At its core, 5S Lean Manufacturing is a systematic approach to workplace organization and standardization. The term “5S” originates from five Japanese words, all starting with the letter ‘S,’ which represent the five pillars of this methodology: Sort (Seiri), Set in Order (Seiton), Shine (Seiso), Standardize (Seiketsu), and Sustain (Shitsuke). These principles aim to create a workplace that is organized, efficient, clean, and free from unnecessary clutter.
Historical Background
5S Lean Manufacturing finds its roots in Japan, where it was developed as part of the Toyota Production System (TPS) during the post-World War II era. Taiichi Ohno, a Toyota engineer, is often credited with pioneering this methodology. The TPS aimed to reduce waste and improve efficiency in manufacturing processes, and 5S played a crucial role in achieving these goals.
The Five Pillars of 5S
1. Sort (Seiri)
The first ‘S’ in 5S stands for “Sort” or “Seiri” in Japanese. This step involves going through all items in the workplace and distinguishing between necessary and unnecessary items. Unnecessary items are removed, creating a clutter-free environment. The goal is to keep only what is essential for daily operations.
2. Set in Order (Seiton)
“Set in Order” or “Seiton” focuses on organizing the necessary items in a logical and efficient manner. Everything has its designated place, and employees can easily locate and access tools, equipment, and materials. This step eliminates wasted time searching for items and minimizes the risk of accidents due to disorganization.
3. Shine (Seiso)
“Shine” or “Seiso” emphasizes the importance of cleanliness and regular maintenance. Workspaces, machinery, and equipment are cleaned thoroughly, ensuring they remain in optimal condition. A clean and well-maintained environment promotes safety, reduces defects, and prolongs the lifespan of assets.
4. Standardize (Seiketsu)
“Standardize” or “Seiketsu” involves establishing standardized procedures and practices for maintaining the first three S’s. Standardization ensures that everyone in the organization follows the same guidelines, creating consistency and reducing the chances of reverting to previous chaotic conditions.
5. Sustain (Shitsuke)
“Sustain” or “Shitsuke” is the ongoing commitment to maintaining the improvements achieved through the previous four S’s. It requires continuous monitoring, employee training, and a culture of discipline to ensure that the workplace remains organized, efficient, and clean over time.
Benefits of Implementing 5S
Now that we’ve covered the fundamental principles of 5S Lean Manufacturing, let’s explore why you should consider implementing this methodology in your organization:
Increased Efficiency
One of the most immediate and tangible benefits of implementing 5S is the increase in efficiency. By sorting and organizing workspaces, employees can quickly locate tools, materials, and equipment they need for their tasks. This reduction in time spent searching for items translates into faster and more efficient processes. Tasks are completed more promptly, production cycles are shortened, and lead times are reduced. As a result, your organization can respond more effectively to customer demands and market changes, gaining a competitive edge in the process.
Improved Safety
Safety is paramount in any workplace, and 5S contributes significantly to creating a safer environment for your employees. An organized and clean workspace minimizes the risk of accidents. There are fewer tripping hazards, no unexpected obstacles, and clear pathways. Additionally, regular cleaning and maintenance as part of the “Shine” principle help identify and address potential safety issues, such as malfunctioning equipment or damaged infrastructure. As a result, your employees can work with peace of mind, knowing that their well-being is a top priority.
Higher Quality
Quality control is vital for any organization, and 5S plays a pivotal role in ensuring higher product or service quality. With reduced clutter and standardized processes, the likelihood of errors and defects is significantly reduced. When tools and materials are readily accessible and workspaces are organized, employees can focus on their tasks without distractions or interruptions. This heightened focus on quality, coupled with the elimination of potential sources of error, leads to consistently higher-quality outputs. Customers notice and appreciate this commitment to quality, which can enhance your organization’s reputation and competitiveness.
Cost Reduction
5S Lean Manufacturing is not just about improving operations; it’s also about optimizing resource usage. By eliminating unnecessary items through the “Sort” principle, you reduce waste and save money on storage space and inventory. Regular maintenance and cleanliness as part of the “Shine” principle help prevent breakdowns and extend the lifespan of machinery and equipment, reducing repair and replacement costs. In essence, 5S leads to cost savings in various aspects of your operations, contributing to improved profitability and financial stability.
Enhanced Employee Morale
A clean and organized workplace contributes to a more pleasant and inviting working environment. When employees see that their organization values cleanliness, orderliness, and efficiency, it can boost their morale and overall job satisfaction. A well-organized workspace reduces frustration and stress, allowing employees to focus on their tasks with a sense of pride in their surroundings. Additionally, when employees are actively involved in the 5S process, they often feel a greater sense of ownership and responsibility for their workspace, further enhancing morale and teamwork.
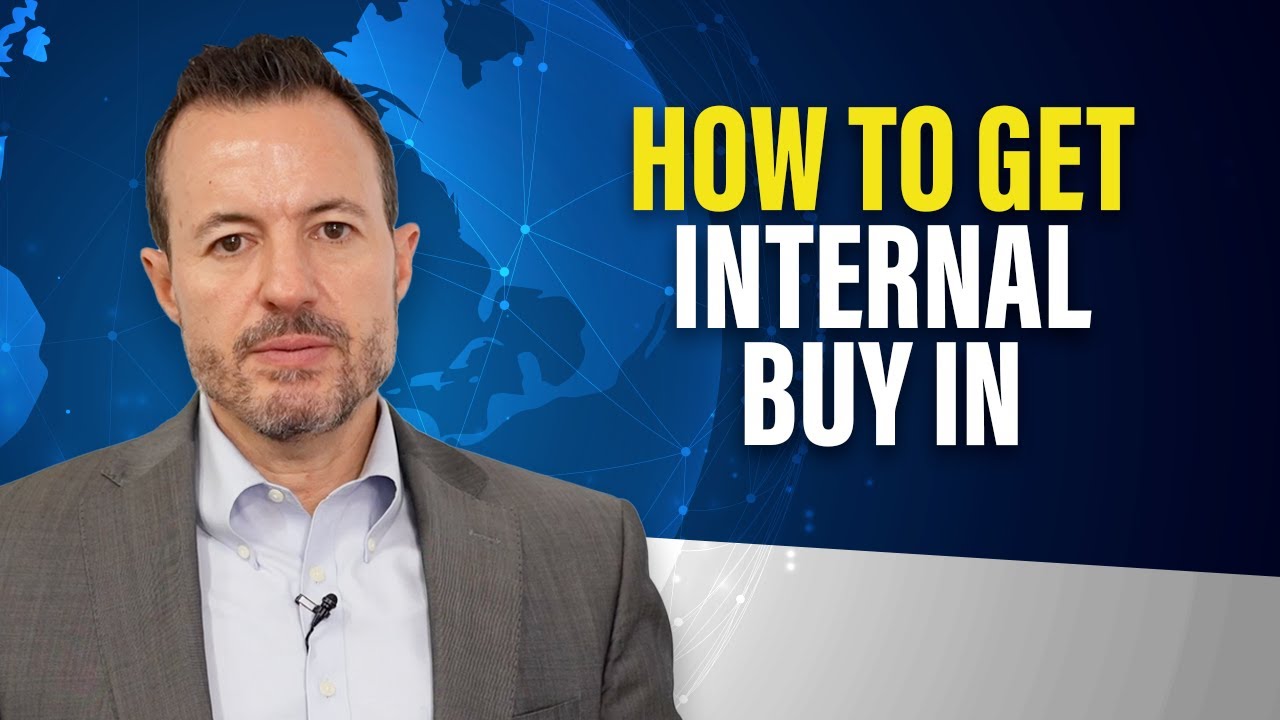
Increased Productivity
Productivity is a crucial metric for any organization, and 5S directly impacts it in a positive way. Streamlined processes and easy access to tools and materials enable employees to work more efficiently. When they don’t have to waste time searching for items or dealing with clutter, they can dedicate more of their time and energy to their core tasks. This translates into increased productivity across the board. Whether you’re in manufacturing, services, or any other industry, improved productivity leads to better output and faster response times, contributing to your organization’s success.
Better Customer Satisfaction
Ultimately, the benefits of 5S Lean Manufacturing translate into better customer satisfaction. Consistent processes and higher product quality mean fewer defects and errors, which directly affect your customers’ experience. A more efficient organization can respond to customer needs and demands more promptly, leading to quicker order fulfillment and delivery. When customers receive high-quality products or services on time, they are more likely to be satisfied and loyal. Additionally, satisfied customers are more likely to recommend your organization to others, potentially boosting referrals and expanding your customer base.
Challenges in 5S Implementation
While the benefits of 5S Lean Manufacturing are compelling, it’s important to acknowledge that implementing this methodology can be challenging. Some common challenges include:
1. Resistance to Change: One of the most common challenges in implementing 5S is resistance to change. Employees may be accustomed to existing work habits and may feel uncomfortable or apprehensive about the changes introduced by 5S. This resistance can manifest as skepticism, pushback, or a reluctance to embrace new practices. It’s essential for organizations to address this resistance through effective communication, involvement of employees in the decision-making process, and providing a clear understanding of the benefits that 5S brings in the long run. Acknowledging the initial disruption and emphasizing the long-term advantages can help ease this challenge.
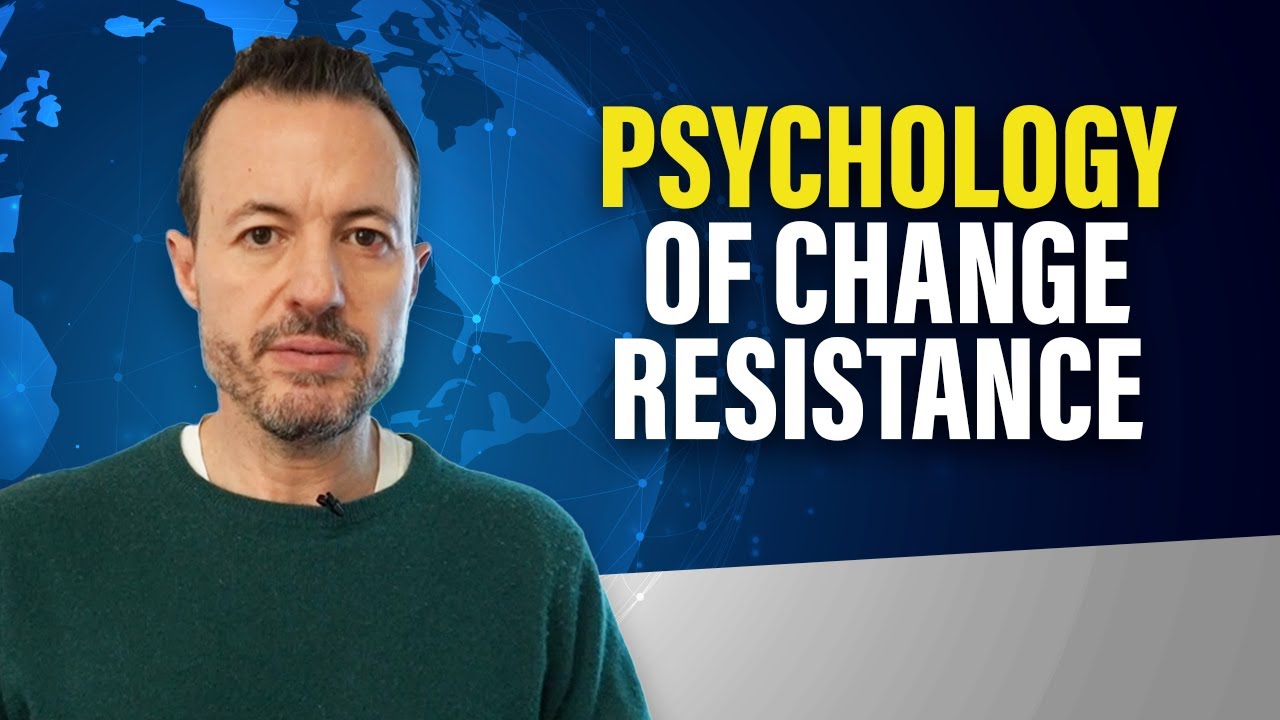
2. Lack of Training: Without proper training, employees may struggle to understand and fully embrace the 5S principles. Each of the five pillars requires a certain level of knowledge and skill to implement effectively. Employees need to know how to sort and categorize items, set them in order, perform proper cleaning and maintenance, standardize processes, and sustain these improvements. Providing comprehensive training programs tailored to the specific needs of different teams within the organization is essential. This education not only equips employees with the necessary tools but also empowers them to actively participate in the 5S journey.
3. Sustainability: Sustaining the improvements achieved through 5S is an ongoing challenge. It’s relatively easy to achieve short-term gains, but maintaining an organized and efficient workplace over the long term requires continuous effort and vigilance. Employees must adopt the 5S principles as part of their daily routines and values. A lack of sustained commitment can lead to regression, where the workplace reverts to its previous disorganized state. To address this challenge, organizations must foster a culture of continuous improvement, provide ongoing training and reinforcement, and regularly assess and adjust their 5S practices.
4. Management Support: Successful 5S implementation often relies heavily on strong support and leadership from management. Without the backing of upper-level management, it can be challenging to drive the necessary changes throughout the organization. Management plays a pivotal role in setting the tone, providing resources, and championing the 5S initiatives. When leaders actively participate in the process and demonstrate their commitment to 5S principles, it sends a powerful message to employees, encouraging their engagement and cooperation. Effective communication from management about the importance and benefits of 5S can also help overcome resistance and gain buy-in from all levels of the organization.

Real-world Examples of 5S Success
To illustrate the effectiveness of 5S Lean Manufacturing, let’s take a look at a couple of real-world success stories:
Toyota:
Toyota, often hailed as the birthplace of 5S Lean Manufacturing, has set a stellar example of how these principles can transform an organization. Toyota’s commitment to 5S has not only shaped its production processes but has also been a cornerstone of its corporate culture.
One of the most notable outcomes of Toyota’s 5S implementation is the creation of highly efficient manufacturing processes. By sorting, setting in order, shining, standardizing, and sustaining their workspaces, Toyota has minimized waste and eliminated unnecessary steps in their production lines. This streamlined approach has significantly reduced lead times, increased production throughput, and enabled just-in-time manufacturing, where parts and materials are delivered precisely when needed. As a result, Toyota can respond swiftly to market demands, produce high-quality vehicles, and maintain low inventory levels.
Furthermore, Toyota’s unwavering dedication to 5S principles has led to the production of high-quality products. The organization’s commitment to cleanliness, orderliness, and standardized processes ensures that their vehicles meet rigorous quality standards consistently. This not only enhances customer satisfaction but also reduces defects and recalls, saving substantial costs associated with rework and warranty claims.
Moreover, Toyota’s reputation for reliability in the automotive industry is strongly linked to its 5S practices. Customers trust Toyota vehicles for their durability and dependability, largely due to the meticulous organization and maintenance of their production facilities. The 5S principles have played a pivotal role in upholding this reputation, contributing to Toyota’s status as a global leader in the automotive industry.
Boeing:
Boeing, a prominent aerospace manufacturer, has successfully applied 5S Lean Manufacturing principles to its production facilities, demonstrating how these principles can be adapted to diverse industries.
By implementing 5S, Boeing has achieved a substantial reduction in waste within its aerospace manufacturing processes. The “Sort” and “Set in Order” principles have enabled Boeing to identify and eliminate redundant inventory, tools, and materials. This reduction in excess resources not only frees up valuable floor space but also reduces costs associated with storage and handling. Boeing’s 5S initiatives have optimized the flow of materials and components, ensuring that they are readily available when needed in the assembly process, which has led to significant efficiency gains.
Boeing’s commitment to safety is also reflected in its 5S practices. The “Shine” principle ensures that workspaces and equipment are well-maintained and regularly cleaned. This proactive approach has not only improved the safety of Boeing’s operations but has also reduced the risk of accidents and injuries, creating a safer environment for its workforce.
Furthermore, Boeing’s 5S implementation has contributed to substantial cost savings. By eliminating waste and optimizing processes, Boeing has reduced operational costs, improved resource utilization, and enhanced overall efficiency. These cost-saving measures have made Boeing more competitive in the aerospace industry, enabling the company to deliver high-quality aircraft at a competitive price point.
In conclusion, both Toyota and Boeing serve as compelling examples of how 5S Lean Manufacturing principles can be successfully integrated into various industries, from automotive to aerospace. These organizations have reaped the benefits of increased efficiency, improved quality, enhanced safety, and cost savings by embracing the 5S methodology. Their experiences showcase the versatility and effectiveness of 5S principles in driving operational excellence and maintaining a strong reputation for reliability and innovation.
How to Start Implementing 5S in Your Organization
Now that you understand the principles, benefits, and challenges of 5S Lean Manufacturing, here are steps to kickstart the implementation process in your organization:
- Assess Current State: Begin by assessing the current state of your workplace. Identify areas that need improvement, potential safety hazards, and sources of waste.
- Form a Cross-functional Team: Create a team with representatives from different departments to ensure diverse perspectives and collective buy-in.
- Training: Provide comprehensive training on the 5S principles to all employees. Ensure they understand the benefits and importance of the methodology.
- Start with Sort: Begin by sorting through items in the workplace and eliminating unnecessary items. This will create the foundation for the subsequent S’s.
- Gradual Implementation: Implement each of the five S’s step by step, allowing time for employees to adjust to the changes.
- Standardization: Develop standardized procedures and practices to maintain the improvements made through the 5S process.
- Sustainability: Foster a culture of sustainability, where all employees are committed to maintaining an organized and efficient workplace.
- Continuous Improvement: Encourage continuous improvement by regularly reviewing and refining your 5S practices.
Conclusion
As you contemplate the integration of 5S principles into your organization, remember that this journey is not a mere checklist of tasks to complete but a transformative voyage. It’s a journey where the destination is not a static point but a dynamic culture of excellence. By embracing 5S, you pave the way for an organizational metamorphosis that transcends processes and systems—it becomes a reflection of your commitment to efficiency, quality, safety, and, above all, the relentless pursuit of excellence. In a world where every advantage counts, 5S Lean Manufacturing is your compass, guiding you toward success, sustainability, and an enduring legacy of excellence in your industry.
I would enjoy brainstorming ideas with you if you are looking to strategize for an upcoming transformation or are looking at selecting an ERP system. Please feel free to contact me at eric.kimberling@thirdstage-consulting.com. I am happy to be a sounding board as you continue your digital transformation journey.